Wrinkle defects and preventive measures for ductile iron castings made with lost foam
1. Formation and prevention of ductile iron castings wrinkle defects
Wrinkle defects often appear at the last place where the molten metal flows or the “cold end” of the liquid flow, generally appearing at the top of the casting, vertical sidewalls or dead corners. The surface of this type of defect is often covered with light and shiny carbon flakes, and the depression of the defect is filled with soot carbon. There are four types of wrinkle defects according to appearance: corrugated, dendritic, dripping and slag inclusion.
1. Formation mechanism
Wrinkle defects are mainly caused by the violent combustion of the pattern material at high temperature and the precipitation of a large amount of free carbon under oxygen conditions. Due to the great difference in density between the molten metal and the free carbon, the free carbon floats to the surface of the molten metal at high temperature or accumulates in a dead corner, and is not discharged in time during the solidification process.
2. Influencing factors
(1) Foam plastic mold material: EPS (expandable polystyrene) is more likely to form wrinkles than EPMMA (expandable polymethyl methacrylate) and STMMA (styrene-methyl methacrylate copolymer resin) because EPS has a higher carbon content than the latter two. EPS contains 92% carbon, STMMA contains 69.6% carbon, and EPMMA contains 60.0% carbon. In addition, the greater the density of the mold, the more liquid products there are after decomposition, and the more likely it is to produce wrinkles.
(2) Influence of chemical composition of castings: For low-carbon cast iron parts, the carbon in the decomposition products of the mold can be partially dissolved in them, and wrinkles are not easy to form; high-carbon cast iron parts (ductile iron castings) are most likely to form wrinkles. This is because at the pouring temperature of ductile iron castings, the foam pattern gasifies to produce a large amount of carbon-containing gas, and about 50% of the pattern weight is precipitated with cracked carbon. In addition, the carbon equivalent and carbon content of ductile iron castings itself are relatively high, so these carbon components are discharged on the surface of the casting or the front of the iron liquid flow, thus forming wrinkles.
(3) Influence of the pouring system: The pouring and riser system has a significant impact on the flow field and temperature field of the iron liquid filling mold, and directly determines the pyrolysis products of the mold material and its flow direction. Increasing the cross-sectional area of the vertical, horizontal and inner runners will easily produce wrinkles (increase in the amount of mold material). The probability of wrinkles in top pouring is lower than that in bottom pouring, so setting a top riser is beneficial to reduce wrinkles.
(4) Influence of casting structure: The smaller the ratio of the volume to the surface area of the casting, that is, the smaller the modulus, the more conducive it is to the discharge of the pattern pyrolysis products, and the smaller the tendency of wrinkle defects.
(5) Influence of pouring temperature: The pouring temperature not only affects the type of pyrolysis products of the pattern material, but also affects the filling speed of the molten metal. When the pouring temperature is lower than a certain critical temperature, the liquid pyrolysis products of the pattern material are dominant, and the filling speed increases with the increase of the pouring temperature; when the pouring temperature is higher than a certain critical temperature, the pyrolysis products are mainly gaseous products, and the filling speed decreases with the increase of the pouring temperature.
(6) Influence of the permeability of the coating layer and the molding sand: The higher the permeability of the molding sand, the more conducive it is to the discharge of the pyrolysis products of the pattern, and the less tendency to form wrinkles. The thinner the coating, and the coarser the particle size of the coating aggregate and the molding sand, the more conducive it is to exhaust and reduce wrinkle defects.
(7) Influence of negative pressure: Increasing the pouring vacuum of cast iron is conducive to smoke and gas exhaust, thereby improving the gasification conditions of the foam plastic, and is conducive to the rapid filling of the mold with molten metal, prompting the escape of residues and gas. However, too high a vacuum is prone to sand sticking defects.
(8) Influence of process coordination: Depending on the size of the casting, the pouring speed should be properly controlled and the vacuum degree should be coordinated. If the coordination is improper, when the pouring speed is increased, the stream becomes thicker, and the vacuum degree is not increased accordingly, wrinkle defects often occur.
3. Preventive measures
During the entire pouring process, efforts should be made to avoid the melting and combustion of foam plastics to prevent the formation of high-temperature decomposition products of foam plastics. It is hoped that it will shrink in volume when it contacts the high-temperature metal and immediately transform into gas and overflow from the mold like sublimation. This is an effective way to eliminate the wrinkles of cast iron parts.
(1) Select suitable foam plastics for casting: In view of the high carbon content of ductile iron castings, which are prone to wrinkles, low-density foam plastic mold materials for casting are selected, such as EPMMA copolymer materials.
(2) Increase the pouring temperature and pouring speed: Increasing the pouring temperature can reduce the wrinkle defect. Since the temperature needs to be reduced by 50~100℃ during the spheroidizing process, in order to ensure the pouring temperature, the molten iron must have a much higher tapping temperature than ordinary gray cast iron, at least 1500℃.
Accelerating the pouring speed (based on the principle of ensuring the smooth flow of molten metal) can make up for the heat loss of foam plastic combustion and gasification in the casting mold, and have sufficient heat energy to ensure the gasification of foam plastic, thereby improving the gasification conditions of foam plastic, which is conducive to the rapid filling of the casting mold with molten metal and promoting the overflow of residues and gas.
(3) Increase the amount of air pumped and the vacuum degree of the casting mold: Practice has proved that with the increase of the negative pressure of the casting mold, it is conducive to reducing or eliminating the wrinkle defect. Because the higher the negative pressure, the faster the filling speed, the shorter the pouring time, resulting in the low viscosity liquid phase product not having time to transform into high viscosity liquid phase decomposition product, and the appearance of bright carbon is reduced; the higher the negative pressure, the more the pyrolysis product of the mold is absorbed and discharged into the molding sand through the coating layer, which is conducive to reducing the wrinkle defect. The recommended vacuum control is: -0.06~-0.09Mpa.
(4) Select a suitable pouring system: According to the characteristics of the foam plastic pattern gasification in the mold, the pouring method of the lost foam casting can be selected from bottom pouring, step pouring, top pouring and rain pouring. However, it must be noted that the metal liquid flow should be stable and quickly fill the mold.
(5) Improve the permeability of the mold: The good permeability of the mold is an important condition to ensure the acquisition of high-quality vacuum lost foam castings. Practice has shown that the main way to improve the permeability of the mold is to use coarse sand, increase the air extraction volume and vacuum degree during pouring, and select reasonable coatings and coating thickness.
(6) Others: Use easily gasified EPS pattern binder. A small amount of cryolite (Na3AlF6) is added to the coating to form highly active NaF, AlF3, etc. at high temperature. These highly active substances can adsorb the carbon decomposed by the pattern, so that it does not precipitate on the surface of the casting, thereby eliminating the wrinkle defect. In addition, adding a certain amount of potassium permanganate to the coating can reduce the wrinkle defects of ductile iron castings and ensure the appearance quality of the castings.
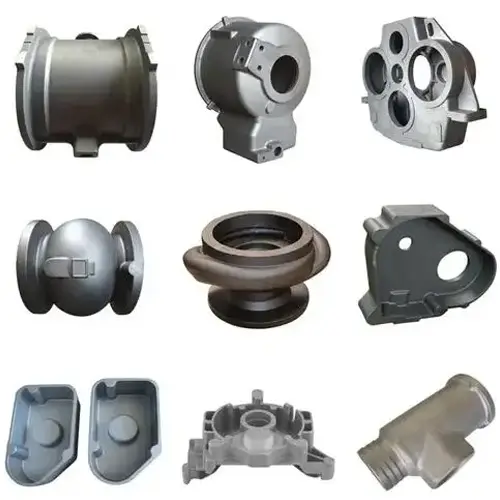