Ductile iron delivers exceptional strength, flexibility, and corrosion resistance, making it the preferred material for water pipes, automotive parts, and heavy machinery components. You benefit from ductile iron’s unique properties that combine the strength of steel with the castability of gray iron, resulting in cost-effective solutions for demanding applications.
Modern industries rely on ductile iron because it offers superior tensile strength up to 80,000 psi while maintaining excellent machinability and weldability. The global ductile iron market reached $5.2 billion in 2023 and continues growing at 4.8% annually, driven by infrastructure development and automotive manufacturing.
Key Takeaways
- Ductile iron combines strength and flexibility, offering 3-5 times the tensile strength of gray iron while maintaining excellent casting properties.
- Water infrastructure applications dominate usage, with ductile iron pipes lasting 100+ years and providing superior corrosion resistance.
- Automotive components benefit from ductile iron’s reliability, including engine blocks, crankshafts, and suspension components.
- Custom ductile iron casting enables specialized applications, from heavy machinery to precision components.
- Cost-effectiveness and sustainability make ductile iron ideal for long-term infrastructure and manufacturing projects.
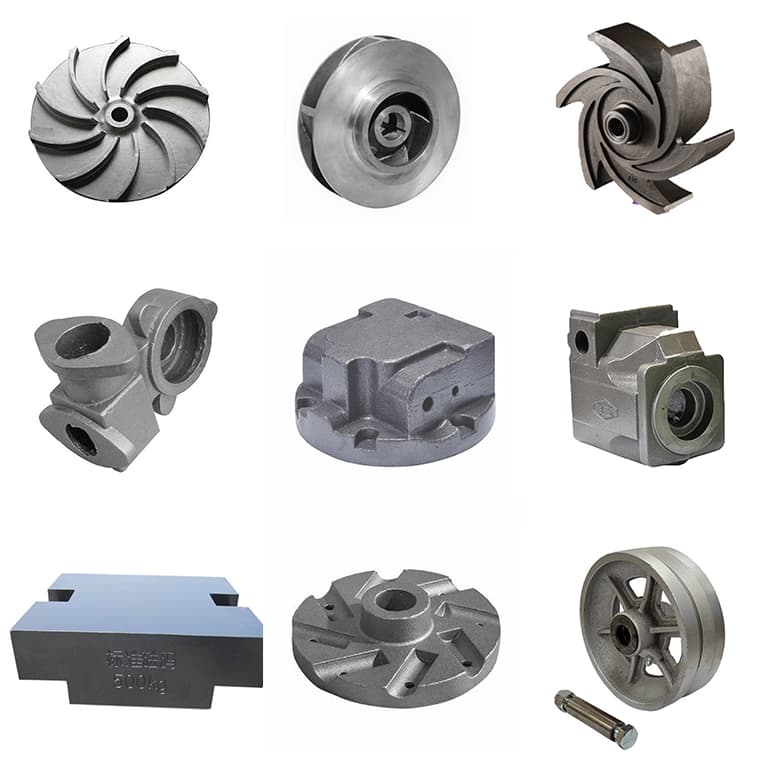
Ductile Iron Overview
What Is Ductile Iron?
You may hear ductile iron referred to as nodular iron or spheroidal graphite iron, but these terms describe the same advanced material. Ductile iron is a type of cast iron where graphite forms spherical nodules instead of flakes, creating superior mechanical properties. This unique microstructure gives ductile iron its characteristic strength and flexibility.
Note: Ductile iron casting produces components with tensile strengths ranging from 60,000 to 120,000 psi, making it suitable for demanding applications where gray iron fails.
The material properties table below shows how ductile iron compares to other cast materials:
Material Type | Tensile Strength (psi) | Yield Strength (psi) | Elongation (%) | Typical Applications |
Ductile Iron | 60,000-120,000 | 40,000-80,000 | 2-18% | Pipes, automotive parts, machinery |
Gray Iron | 20,000-50,000 | N/A | <1% | Engine blocks, brake drums |
Steel | 50,000-200,000 | 30,000-150,000 | 10-30% | Structural components, tools |
Aluminum | 10,000-70,000 | 5,000-60,000 | 2-20% | Aerospace, automotive lightweight parts |
These measurable standards help you choose the right material for your specific application. Ductile iron casting must meet ASTM standards such as A536 to ensure quality and performance.
How Ductile Iron Works
Ductile iron achieves its superior properties through controlled metallurgy. You create ductile iron by adding magnesium or cerium to molten iron during the casting process. These additives cause graphite to form as spheres rather than flakes, eliminating stress concentrations that weaken gray iron.
The spherical graphite structure provides several advantages:
- Enhanced ductility allows the material to bend without breaking.
- Improved impact resistance prevents catastrophic failure under shock loads.
- Better machinability reduces manufacturing costs and improves surface finish.
- Excellent castability enables complex shapes and thin sections.
You benefit from ductile iron’s unique combination of properties in multiple ways:
Strength and durability: Ductile iron resists wear, fatigue, and thermal cycling better than gray iron or aluminum alternatives.
Design flexibility: The material’s excellent casting properties allow you to create complex geometries that would be expensive or impossible with other materials.
Cost-effectiveness: Ductile iron provides steel-like performance at cast iron prices, reducing both material and manufacturing costs.
Sustainability: The material’s longevity and recyclability support environmental goals while providing reliable long-term performance.
Tip: Custom ductile iron casting allows you to optimize component design for specific applications, potentially reducing weight while maintaining strength.
Recent industry developments highlight ductile iron’s growing importance:
- Infrastructure replacement projects increasingly specify ductile iron for water and sewer systems
- Automotive manufacturers use ductile iron for lightweighting initiatives without sacrificing durability
- Wind energy applications leverage ductile iron’s fatigue resistance in turbine components
- The material’s corrosion resistance makes it ideal for marine and chemical processing applications
When you plan a ductile iron project, consider these factors:
- Grade selection based on required strength and ductility
- Section thickness affects cooling rate and mechanical properties
- Heat treatment can modify properties for specific applications
- Surface treatments enhance corrosion resistance when needed
- Quality control ensures consistent properties throughout the casting
Ductile iron casting provides the versatility, performance, and cost-effectiveness modern industries demand. You can support heavy loads, resist corrosion, and maintain dimensional stability—all with one adaptable material system.
Applications of Ductile Iron
Water and Sewer Systems
Pipe Infrastructure
You find ductile iron pipes in municipal water systems worldwide because they provide unmatched durability and corrosion resistance. These pipes handle high-pressure applications up to 350 psi while maintaining structural integrity for over 100 years. The material’s flexibility allows it to withstand ground movement and thermal expansion without cracking.
Modern ductile iron pipes feature advanced protective coatings:
- Polyethylene encasement protects against soil corrosion
- Cement mortar lining prevents internal corrosion and maintains flow capacity
- Epoxy coatings provide additional protection in aggressive environments
Fittings and Valves
Ductile iron fittings complement pipe systems with matching durability and pressure ratings. You benefit from standardized designs that ensure proper fit and long-term reliability. Common fittings include:
- Tees and crosses for system branching
- Reducers for pipe size transitions
- Flanged adapters for equipment connections
- Valve bodies for flow control applications
Automotive Applications
Engine Components
Ductile iron engine blocks deliver superior strength-to-weight ratios compared to gray iron alternatives. You achieve better thermal management and reduced noise, vibration, and harshness (NVH) characteristics. The material’s excellent machinability reduces manufacturing costs while maintaining precise tolerances.
Crankshafts made from ductile iron provide exceptional fatigue resistance under high-stress conditions. The material’s ductility prevents catastrophic failure modes common in brittle materials.
Suspension and Chassis Parts
Ductile iron suspension components offer reliable performance in demanding automotive applications:
- Control arms benefit from the material’s impact resistance
- Steering knuckles utilize ductile iron’s strength and machinability
- Brake calipers leverage thermal stability and corrosion resistance
Tip: Custom ductile iron casting enables automotive manufacturers to optimize component design for specific vehicle platforms while maintaining cost-effectiveness.
Industrial and Heavy Machinery
Mining and Construction Equipment
Heavy-duty applications demand ductile iron’s combination of strength, wear resistance, and repairability. You find this material in:
- Excavator components that withstand abrasive conditions
- Crusher parts requiring impact and wear resistance
- Conveyor system components needing long-term reliability
Manufacturing Equipment
Ductile iron provides stable platforms for precision manufacturing:
- Machine tool beds benefit from excellent vibration damping
- Gear housings utilize the material’s strength and machinability
- Hydraulic components leverage pressure, resistance, and durability
Specialized Applications
Wind Energy
Wind turbine applications utilize ductile iron’s fatigue resistance and environmental durability:
- Hub castings support massive rotor assemblies
- Nacelle components withstand constant vibration and weather exposure
- Foundation anchor systems provide long-term structural integrity
Marine and Offshore
Saltwater environments challenge materials, but ductile iron with proper protective coatings delivers reliable performance:
- Propeller hubs resist corrosion and impact damage
- Hull fittings maintain watertight integrity under pressure
- Offshore platform components provide structural support in harsh conditions
The versatility of ductile iron casting makes it suitable for diverse applications across multiple industries. You can specify this material with confidence for both standard and custom applications requiring superior mechanical properties.
Types of Ductile Iron Casting
Standard Ductile Iron Grades
You select from several standard ductile iron grades based on your application requirements. Each grade offers specific combinations of strength, ductility, and hardness optimized for different uses.
Grade 60-40-18 provides good ductility for general applications requiring moderate strength. You typically use this grade for pipe fittings and automotive components where impact resistance matters.
Grade 65-45-12 offers balanced properties for structural applications. This grade suits machine components and heavy-duty castings requiring reliable performance.
Grade 80-55-06 delivers high strength for demanding applications. You choose this grade for engine blocks, crankshafts, and other high-stress components.
Grade 100-70-03 provides maximum strength for extreme applications. This grade handles the most demanding conditions in mining and heavy industrial equipment.
Grade | Tensile Strength (ksi) | Yield Strength (ksi) | Elongation (%) | Typical Applications |
60-40-18 | 60 | 40 | 18 | Pipe fittings, general castings |
65-45-12 | 65 | 45 | 12 | Machine components, structural parts |
80-55-06 | 80 | 55 | 6 | Engine blocks, high-stress components |
100-70-03 | 100 | 70 | 3 | Mining equipment, extreme applications |
Custom Ductile Iron Casting
Custom ductile iron casting allows you to optimize component design for specific applications. You work with foundries to develop unique solutions that standard products cannot provide. This approach enables:
- Tailored mechanical properties through alloy modifications and heat treatment
- Complex geometries that integrate multiple functions into a single component
- Optimized wall thickness for weight reduction without strength compromise
- Specialized surface treatments for enhanced corrosion or wear resistance
Design Considerations for Custom Casting
When you develop custom ductile iron castings, consider these factors:
Section thickness affects cooling rate and mechanical properties. Thicker sections cool slower, potentially reducing strength but improving ductility.
Ribs and reinforcement optimize strength-to-weight ratios. You can design internal structures that maximize performance while minimizing material usage.
Draft angles and fillet radii improve castability and reduce stress concentrations. Proper design reduces manufacturing costs and improves component reliability.
Machining allowances account for surface finishing requirements. You specify additional material where precise dimensions or surface finish are critical.
Quality Control in Custom Casting
Custom ductile iron casting requires rigorous quality control to ensure consistent properties:
- Chemical analysis verifies alloy composition meets specifications
- Mechanical testing confirms tensile strength, yield strength, and elongation
- Metallographic examination ensures proper graphite structure
- Dimensional inspection validates geometric accuracy
- Non-destructive testing detects internal defects
Note: Qualified foundries follow ISO 9001 standards and industry-specific certifications to ensure consistent quality in custom ductile iron casting projects.
Specialized Casting Processes
Sand Casting
Traditional sand casting remains the most common method for ductile iron production. You benefit from:
- Cost-effective tooling for low to medium production volumes
- Design flexibility for complex internal geometries
- Large component capability for heavy machinery applications
- Established quality procedures with proven results
Investment Casting
Investment casting produces precision components with an excellent surface finish. This process suits applications requiring:
- Tight tolerances without extensive machining
- Complex internal passages for hydraulic or pneumatic systems
- Superior surface quality for appearance or functional requirements
- Near-net-shape components that minimize material waste
Die Casting
Die casting enables high-volume production of smaller ductile iron components. You achieve:
- Consistent dimensional accuracy across large production runs
- Reduced machining requirements through precision casting
- Lower per-unit costs for high-volume applications
- Excellent surface finish directly from the casting process
The choice of casting process depends on your specific requirements for volume, precision, complexity, and cost. Professional foundries help you select the optimal approach for your custom ductile iron casting needs.
Ductile Iron Selection and Processing
Choosing the Right Grade
You need to match your ductile iron grade to your application’s specific requirements. Start by evaluating these critical factors:
Load requirements: Determine maximum static and dynamic loads your component will experience. High-stress applications require grades 80-55-06 or 100-70-03.
Impact resistance: Components subject to shock loads benefit from grades with higher elongation values like 60-40-18 or 65-45-12.
Environmental conditions: Corrosive environments may require specialized grades with enhanced resistance or protective coatings.
Machinability needs: Consider post-casting machining requirements. Lower-strength grades typically machine more easily.
Cost considerations: Balance performance requirements with budget constraints. Higher-strength grades cost more but may provide better long-term value.
Temperature exposure: Evaluate operating temperature ranges. Some applications may require heat treatment or special alloy modifications.
Heat Treatment Options
Heat treatment modifies ductile iron properties to meet specific application requirements. You can choose from several treatment methods:
Annealing
Annealing improves ductility and machinability by reducing hardness. You use this treatment for components requiring extensive machining or forming operations.
Normalizing
Normalizing refines grain structure and improves strength uniformity. This treatment suits structural applications where consistent properties are critical.
Quenching and Tempering
Quenching and tempering maximize strength and hardness while maintaining adequate ductility. You apply this treatment to high-stress components like gears and shafts.
Austempering
Austempering produces austempered ductile iron (ADI) with exceptional strength and toughness. This treatment creates components with steel-like properties at a lower cost.
Treatment | Typical Hardness (HB) | Tensile Strength (ksi) | Applications |
As-cast | 150-250 | 60-80 | General components |
Annealed | 120-180 | 50-70 | Machined parts |
Normalized | 180-280 | 70-90 | Structural components |
Quenched & Tempered | 250-400 | 90-150 | High-stress parts |
Austempered | 300-450 | 120-200 | Premium applications |
Quality Assurance
Quality control ensures your ductile iron components meet specifications consistently. Comprehensive testing includes:
Chemical analysis verifies carbon, silicon, magnesium, and other element levels. Proper chemistry ensures nodular graphite formation and desired properties.
Tensile testing confirms strength, yield point, and elongation meet grade requirements. Standard test bars represent actual casting properties.
Hardness testing validates heat treatment effectiveness and material consistency. Rockwell or Brinell measurements provide quick property assessment.
Metallographic examination reveals graphite structure, matrix composition, and potential defects. This microscopic analysis ensures proper material structure.
Dimensional inspection verifies geometric accuracy and surface quality. Coordinate measuring machines (CMMs) provide precise measurements for critical features.
Non-destructive testing detects internal defects without damaging parts. Ultrasonic, magnetic particle, or dye penetrant methods reveal hidden flaws.
Tip: Work with certified foundries that maintain ISO 9001 quality systems and follow industry-specific standards for consistent results.
Processing Considerations
Successful ductile iron processing requires attention to several factors:
Melting practice affects final properties. Proper temperature control, desulfurization, and inoculation ensure quality castings.
Pouring procedures influence casting integrity. Controlled pouring prevents turbulence and oxide inclusion formation.
Cooling control manages solidification to achieve the desired properties. Proper cooling prevents defects and ensures uniform structure.
Cleaning and finishing prepare castings for use. Shot blasting, grinding, and machining remove surface irregularities and achieve final dimensions.
Inspection protocols verify quality at each stage. In-process monitoring prevents defects and ensures consistent output.
When you plan your ductile iron project, consider these processing requirements early in the design phase. Proper material selection and processing ensure your components deliver expected performance and reliability.
Conclusion
Ductile iron provides the ideal combination of strength, flexibility, and cost-effectiveness for modern industrial applications. You gain access to a material that delivers steel-like performance at cast iron prices while offering superior design flexibility and manufacturing efficiency.
The material’s proven performance in water infrastructure, automotive applications, and heavy machinery demonstrates its reliability across diverse industries. From municipal pipe systems lasting over 100 years to precision automotive components handling extreme stresses, ductile iron consistently delivers exceptional value.
When you need reliable, cost-effective casting solutions that combine strength with manufacturability, choose a proven ductile iron casting foundry. Shengrong offers the expertise, quality systems, and technical support necessary to deliver superior ductile iron components for your most demanding applications.
FAQ
What makes ductile iron different from regular cast iron?
Ductile iron contains spherical graphite nodules instead of flakes, providing 3-5 times the tensile strength and significantly better ductility than gray iron.
How long do ductile iron components last?
Properly designed and manufactured ductile iron components can last 50-100+ years, depending on application and environmental conditions.
Can ductile iron be welded?
Yes, ductile iron can be welded using appropriate procedures and filler materials. Preheating and post-weld heat treatment may be required for optimal results.
What industries use ductile iron most?
Water utilities, automotive manufacturing, heavy machinery, and construction industries are the largest consumers of ductile iron castings.
How do you specify the right ductile iron grade?
Consider load requirements, impact resistance needs, environmental conditions, and cost constraints when selecting from standard grades 60-40-18 through 100-70-03.