Home > Gray cast iron parts
Shengrong gray cast iron parts features
Shengrong iron casting parts based on standard EN1561-2011,surface smooth, dimensions accurate, actual weight no more 3% difference of theoretical weight, chemical composition meets the standards, no pores, no slag inclusions, no shrinkage holes inside, casting parts more stranger and good wear resistance than other factory
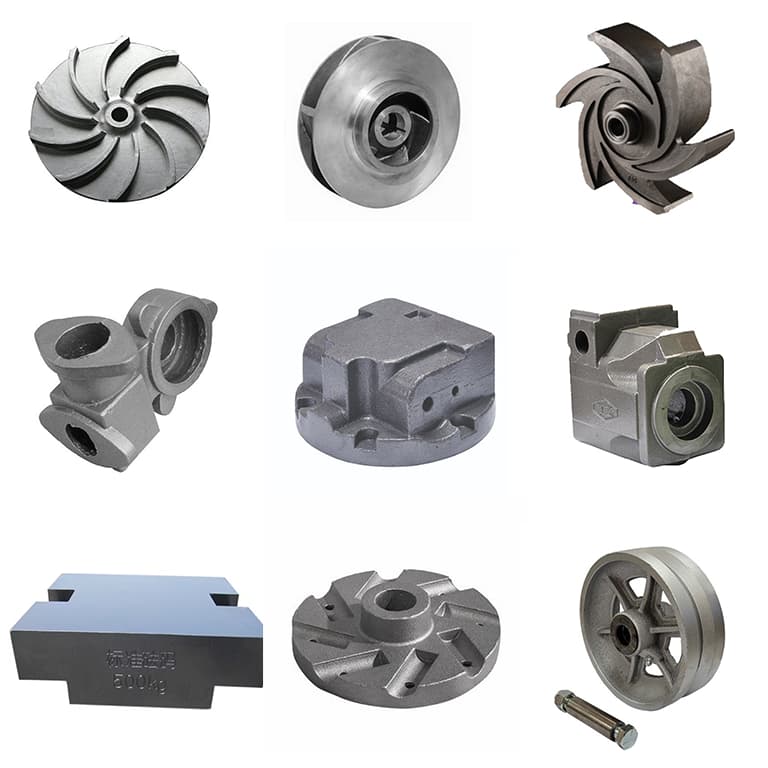
Why choose shengrong gray cast iron parts?
1:Shengrong casting foundry production capacity can meet your different size, weight from 0.5-10000kgs,the surface smooth, dimension aacurate,exzactly weight, casting parts no pores and defects, more stronger and resistance
2.Shengrong no MOQ requirement. For small order or samples, we make casting parts with lost foam castings-it is economic way. For big order, we make aluminum mold, quality more better
3.Shengrong carefully inspection of casting parts, test as tension, yield, and elongation, Non-destructive testing, and other test requirement as customer need.
4.Shengrong iron casting parts delivery time more quickly. For samples, 15-20days. For bulk order no more than 35 days. Samples free, you just only pay mold cost and air express shipping price.
5.Shengrong foundry packing in woodbox packing with anti-rust oil,can keep the casting parts in good condition after long time shipping
6.Shengrong foundry promiss 95% pass rate of our products. If less than this rate, we will send you new casting parts to replace the defects products
Typical Case Of Cast Iron Parts


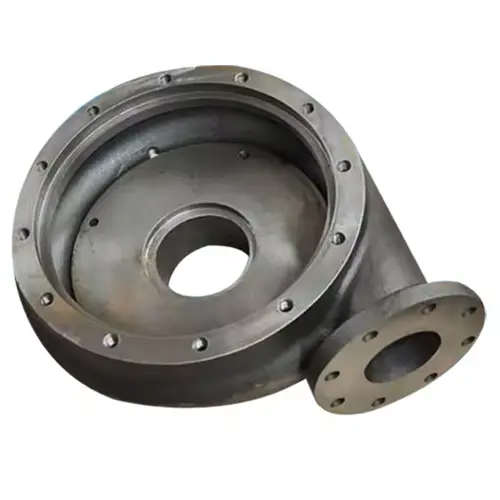


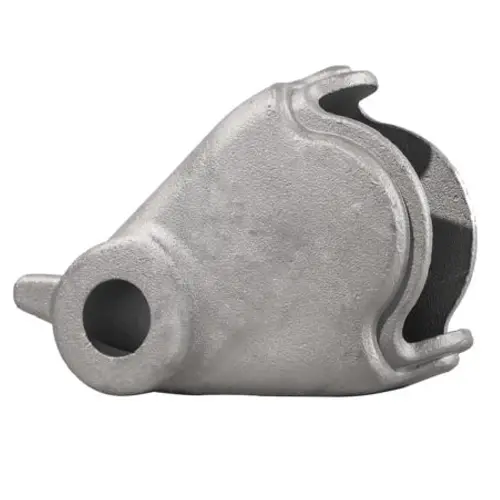
Comparison table of gray iron grades in various countries
You can choose a best material for you
Gray Iron Material Grades | ||||||||
Country | Standard | Equivalent Grades of Grey Iron (Gray Cast Iron) | ||||||
ISO | ISO 185 | 100 | 150 | 200 | 250 | 300 | 350 | – |
China | GB 9439 | HT100 | HT150 | HT200 | HT250 | HT300 | HT350 | – |
USA | ASTM A48 | – | NO.20 | NO.30 | NO.35 | NO.40 | NO.50 | NO.55 |
NO.25 | NO.45 | NO.60 | ||||||
Germany | DIN 1691 | GG10 | GG15 | GG20 | GG25 | GG30 | GG35 | GG40 |
European | EN 1561 | EN-GJL-100 | EN-GJL-150 | EN-GJL-200 | EN-GJL-250 | EN-GJL-300 | EN-GJL-350 | |
Japan | JIS G5501 | FC100 | FC150 | FC200 | FC250 | FC300 | FC350 | – |
Italy | UNI 5007 | G10 | G15 | G20 | G25 | G30 | G35 | – |
France | NF A32-101 | – | FGL150 | FGL200 | FGL250 | FGL300 | FGL350 | FGL400 |
UK | BS 1452 | 100 | 150 | 200 | 250 | 300 | 350 | – |
India | IS 210 | – | FG150 | FG200 | FG260 | FG300 | FG350 | FG400 |
Spain | UNF | – | FG15 | FG20 | FG25 | FG30 | FG35 | – |
Belgium | NBN 830-01 | FGG10 | FGG15 | FGG20 | FGG25 | FGG30 | FGG35 | FGG40 |
Australia | AS 1830 | – | T150 | T220 | T260 | T300 | T350 | T400 |
Sweden | SS 14 01 | O110 | O115 | O120 | O125 | O130 | O135 | O140 |
Norway | NS11 100 | SJG100 | SJG150 | SJG200 | SJG250 | SJG300 | SJG350 | – |
Min. Tensile Strength (Mpa) | 100 | 150 | 200 | 250 | 300 | 350 | – |
Sand casting process and equipment
Design and produce molds
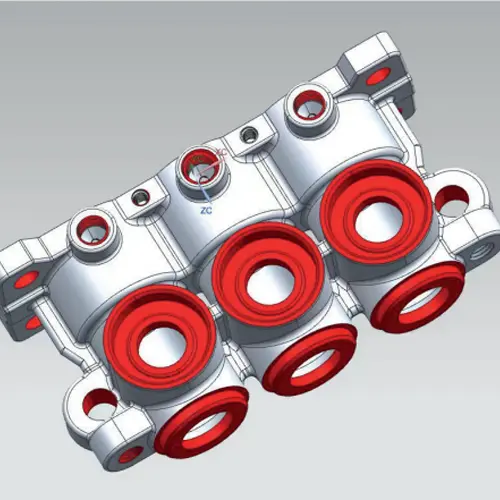
We have established an engineering technology materials R&D center to invest more in product development and technological innovation. In line with the CAD and UG three-dimensional mold creation capabilities equipped with independent R&D, we can reduce design defects, improve casting quality, and improve product processing and casting methods, technologies and The improvements and innovations in the process have made Shengrong a complete solution provider in the high-end casting industry that integrates R&D and production.
Cast Star Horizontal Molding Line
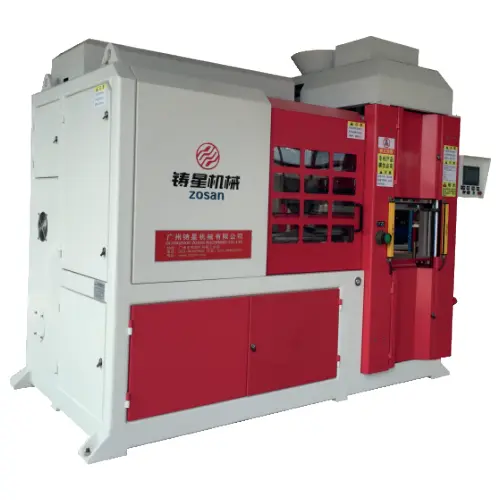
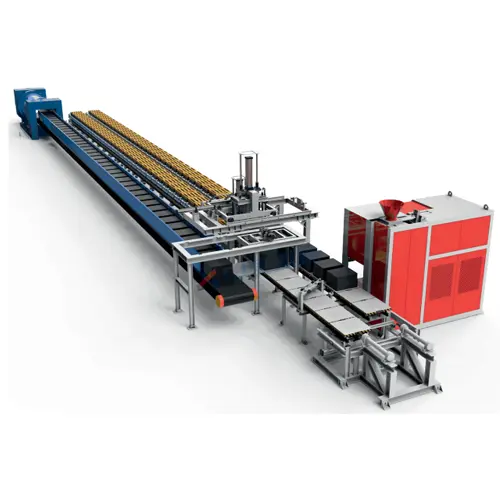
Sinto Molding Machine
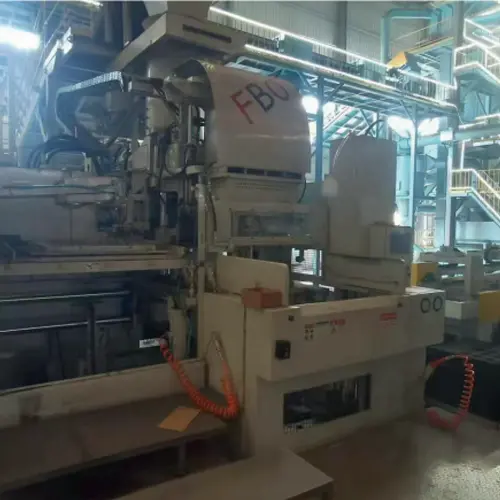
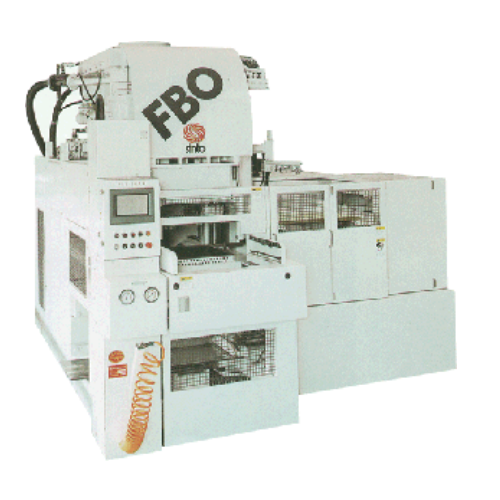
Coremaking machine

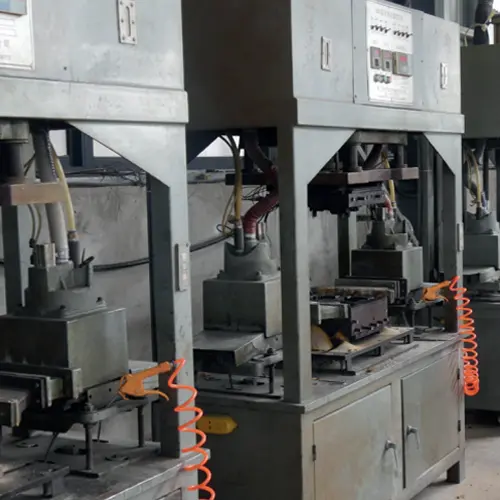
Melting and pouring
1T intermediate frequency furnace 3 sets.

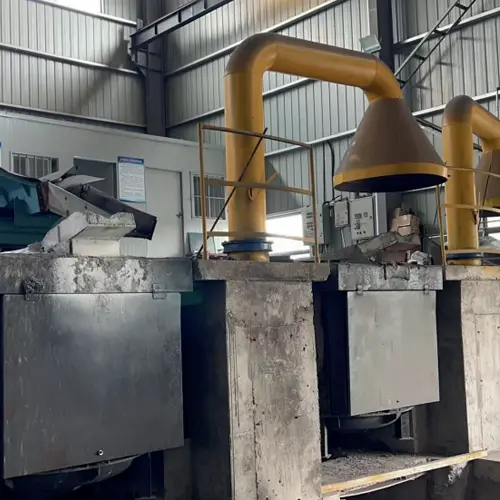
Cleaning and heat treatment
Heat treatment furnaces
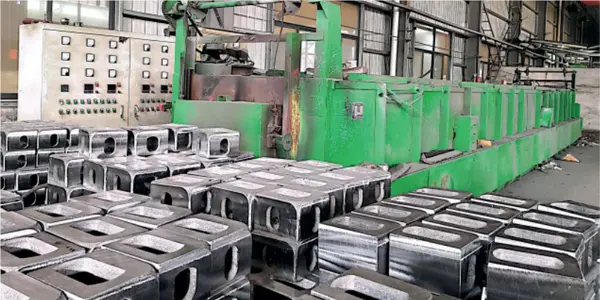
Machining centers
20 machining centers for casting parts
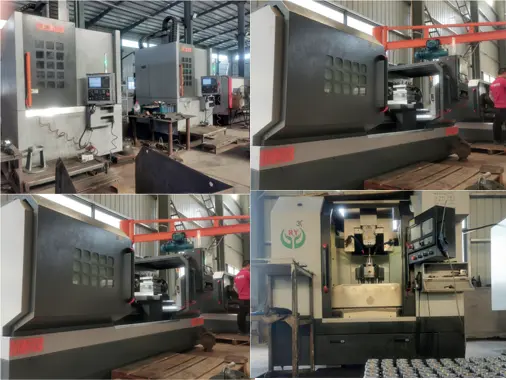
Inspetion and testing of cast iron parts
we have independent physical and chemical testing laboratory. The main testing equipment includes: 2 spectrometers, 2 universal material testing machines, C-S analyzer, Si-Mn-P high-speed analyzer, 2 metallographic microscopes, 2 Brinell hardness meters, impact testing machines, molding sand permeability detectors, independent physical and chemical testing laboratory,air permeability tester for molding sand, tensile tester for molding sand, high-frequency infrared moisture detector, ultrasonic flaw detector and various equipment. Sand tensile test detector, high-frequency infrared moisture detector, ultrasonic flaw detector and all kinds of equipment are complete.
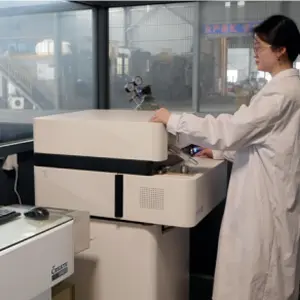

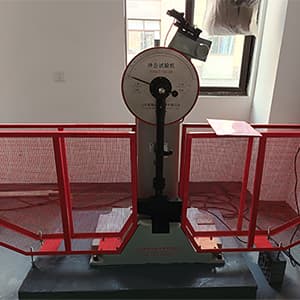
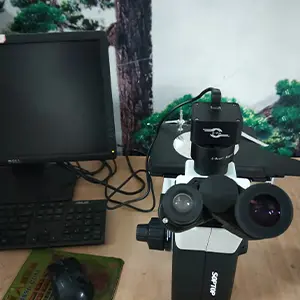
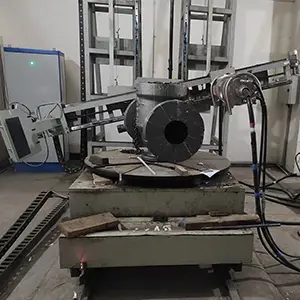
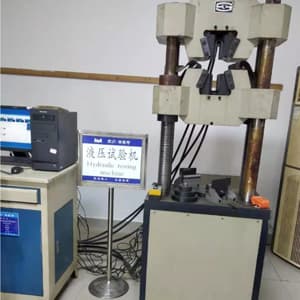
Spectrometer
Carbon sulfur analyzer
Impact tester
Metallurgical microscope
Radial inspection machine
Hydraulic universal testing machine
The production of gray cast iron parts
1: What casting process you offer?
We use sand casting, lost foam casting, resin sand casting and other process to make gray cast iron parts
2: What size of the parts you are making?
We make the parts from 0.5kgs to 10000kgs, special size is available
3: What the lead time of production?
For samples, it need about 30days(model develop time 15-20 days, samples production time 10 days)
Bulk order after mold finished, it need about 20 days
4: What capacity do you have?
Our yearly production can reach to 4000 tons
5:Can you do the machining as our drawing?
Yes, please offer detailed 2D drawing
6: What about your after service?
We promise the QC pass rate 95%, if lower than this, we will send you new part free of charge