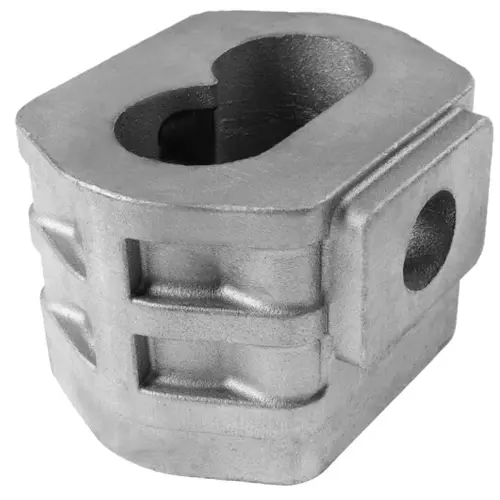

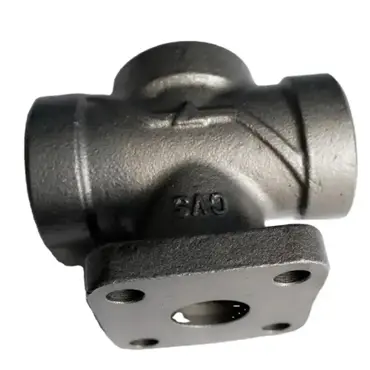
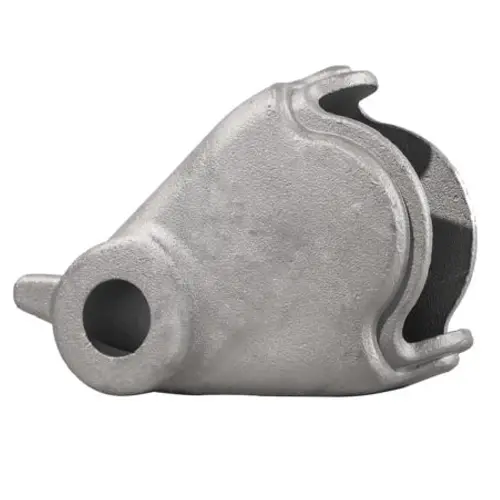
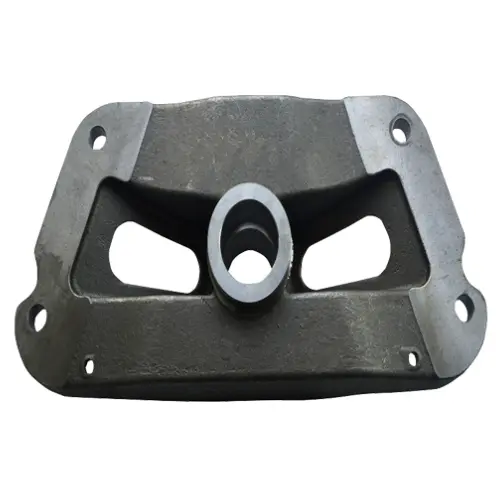
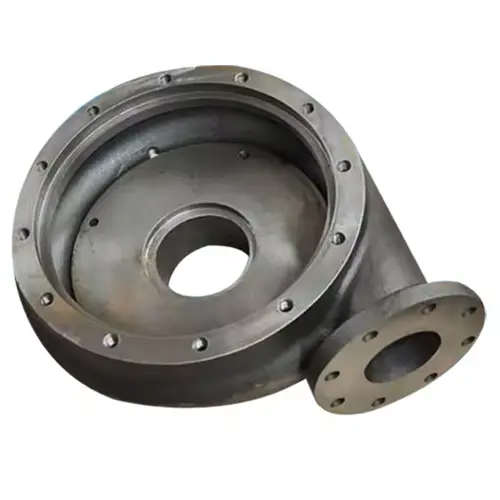
Construction machinery castings refer to casting parts used to manufacture construction machinery. Construction machinery includes various heavy equipment such as excavators, loaders, bulldozers, road rollers, concrete mixers, etc., and castings are one of the important components of these machines. Castings are parts made by casting processes, and they are usually made of metal or alloy materials. In the field of construction machinery, common castings include fuselages, frames, booms, bucket teeth, track sprockets, etc.
The production process of casting can be divided into several key steps
1. Mold making
The mold is the first step of casting, and a good mold directly affects the final quality of the casting. The mold can be made of metal or other materials, and is usually designed according to the shape and size of the casting. In this process, the designer needs to carefully consider factors such as the cooling rate and shrinkage of the casting to ensure the accuracy of the mold.
2. Batching and smelting
Batching and smelting are the core links of casting. Different engineering machinery castings require molten metal of different compositions, so strict proportions are essential in this step. Melting is usually carried out in a high-temperature furnace, and impurities need to be continuously removed during the smelting process to ensure the purity of the molten metal.
3. Casting
The next step is casting, pouring the molten metal into the mold. This step seems simple, but it is actually a manifestation of technology. The casting speed, temperature control, and the fluidity of the molten metal will affect the molding of the casting. Imagine that just like pouring water, the speed and direction of the water flow will affect the filling degree of the cup.
4. Cooling and demolding
The cooling time of the casting in the mold cannot be ignored. Cooling too quickly may cause cracks in the casting, while cooling too slowly will affect production efficiency. Therefore, reasonable cooling time and methods need to be adjusted according to different materials and shapes. The demolding operation should also be cautious to avoid damaging the newly formed casting.
5. Post-processing
The last step is to post-process the casting, including cleaning, polishing and surface treatment. These steps not only improve the appearance of the casting, but also enhance its corrosion resistance and wear resistance. Imagine a brand new casting, after post-processing, like a work of art, glowing with a charming luster.
Casting quality control
In the production process, quality control is an important link that cannot be ignored. In order to ensure that every engineering machinery casting meets the standards, multiple tests are usually carried out. This includes metal composition analysis, mechanical properties testing, etc. It’s like taking a rigorous exam, and every link must be refined.
Ductile iron is carbon in the form of spherical graphite. Its mechanical properties are far superior to those of gray iron and close to those of steel. It has excellent casting, cutting and wear resistance, and has a certain degree of elasticity. It is widely used in the manufacture of high-end castings such as crankshafts, gears, pistons, and various mechanical parts.
Details
Details:
Model
Material
Brand
Origin
Application
Construction machine castings
Ductile Iron QT450-10
Shengrong
China
Engine cylinder block, track plate, booms and other parts
Sand Casting in Engineering Machinery
Sand casting: A casting process in which molten liquid metal is formed in a sand mold. Steel, iron and most nonferrous alloy castings can be obtained by sand casting. Since the molding materials used in sand casting are cheap and easy to obtain, and the mold is easy to manufacture, it is suitable for single-piece production and small-batch production of castings. It has long been the basic process in metal casting production. Castings are widely used in engineering machinery, mainly used to produce various structural parts, mechanical parts and functional parts. The following are several typical application scenarios:
1. Engine cylinder block, crankcase, cylinder head and other parts.
2. Track plate, sprocket, drive gear and other parts in the walking system.
3. Shovel teeth, buckets, bucket teeth, rods and other parts in the excavation device.
4. Booms, wire rope pulleys, balance frames and other parts in lifting machinery.
The whole process of casting production includes mold making, sand mold making, furnace smelting, metal pouring, cooling and sand removal, size inspection and other steps. Among them, mold making is the first link in casting production, and different parts need to design different molds. Sand mold making refers to filling specific sand in the mold to form a sand mold with a specific shape. Furnace smelting refers to melting the metal into a liquid state to form cast iron liquid or cast steel liquid, and adding a certain amount of ferrite and steel agent. Metal pouring refers to pouring cast iron liquid or cast steel liquid into the mold, and forming a casting after solidification and cooling. Cooling and sand removal refers to cooling the casting to room temperature, removing the mold and sand, and then performing related treatments, such as deburring and grinding. Dimensional inspection refers to the inspection of the casting in terms of size, shape, weight, etc.